- Home
- >>
- Capabilities & Services
MECHANICAL DESIGN AND ANALYSIS CAPABILITIES
FMB has established three departments representing the engineering and scientific competencies of the company:
- Development
- Design
- Control Systems.
Highly qualified engineers and physicists are able to realise your ideas and perform the full range of design and analysis work, including:
- Mechanical Design
- Motion System Design
- Optical Design
- Radiation Monitoring Design
- Electrical Design
- Thermal Analysis
- Stress Analysis
- Vibration Analysis
- Optical Ray Tracing
- Bremsstrahlung Tracing
- Vacuum Calculation
- Finite Element Analysis
- Temperature Stability, Flow rates
- and Pressure Drop Calculation
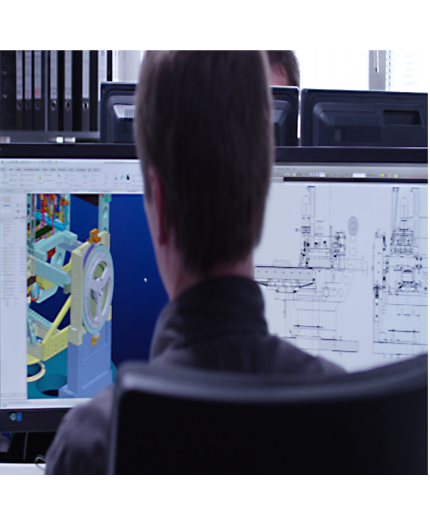
MANUFACTURING CAPABILITIES
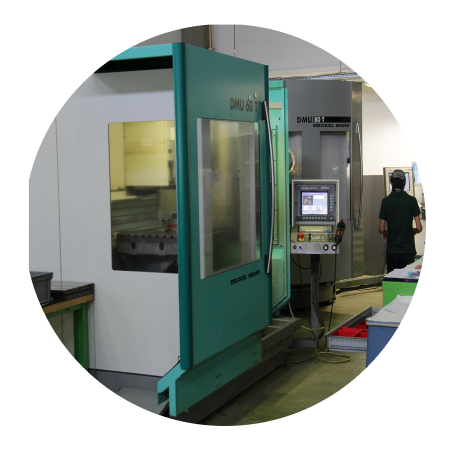
Mechanics
Turning, milling, drilling and grinding are all done both on conventional machines and also on CNC machine tools.
- Lathing
- Components of up to 1m in diameter and 2m in length
- Milling
- Components of up to 1.5m x 1.5m x 0.8m
- Drilling
- Sheet Machining
- Cutting
- Bending and Rolling
- In Cooperation
- High pressure jet cutting
- Laser cutting
- Plate bending
- Deep drawing
Welding
- Tungsten Insert Gas (TIG) welding
- Microplasma welding
- Metal Activ Gas (MAG) arc welding
- Vacuum brazing / High-Vacuum
- Heat Treatment Furnace
- Additional
- - separate room for glass ball blasting
- - separate clean room ISO 6 especially for welding (8 m2)
- In Cooperation (done by experienced Partners)
- Electron beam welding
- Laser welding
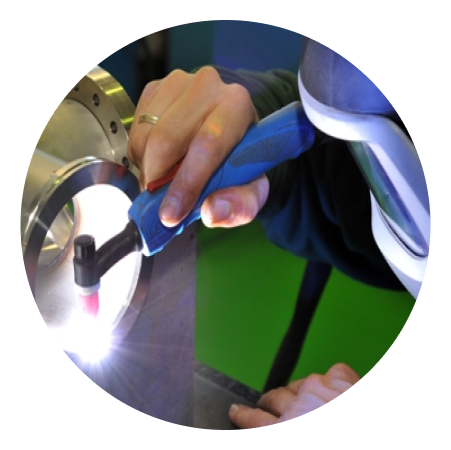
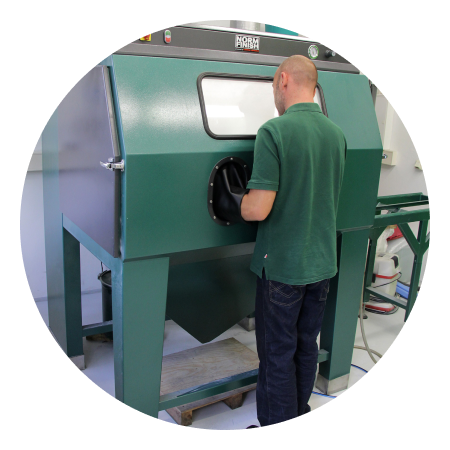
Assembly and adjustment
FMB ensures its equipment meets the high requirements in terms of cleanness and purity by conducting assembly in separate, low-particle-count or clean rooms.
- Appropriate assembly halls, including one dust free clean room, are available for UHV–proof assembly.
- High–precision theodolites are available for adjustment and high– precision position control of components and comple
High-Vacuum Heat Treatment Furnace
High-quality soldering work is done in our own clean high-vacuum furnace. FMB can also offer the right quality when soldering different materials and combinations of high-grade steel, copper, Glidcop or ceramic.
We are able to offer the following technologies and services :
- UHV–proof brazing on components made of copper, Glidcop, Stainless Steel, Molybdenum, Tungsten, Mu–metal, Ceramics
- Brazing under partial pressure (Ar and N2)
- Stress relief annealing
- Annealing for reduction of residual permeability
Technical Data:
- Brazing area dimensions (wxhxd): 500 x 500 x 800 mm3
- Dimensions of parts (max) (wxhxd): 600 x 600 x 1000 mm3
- Temperature measurements on components: at 9 Positions
- Uniformity of temperature in the brazing area: <+/– 5 K
Request Data Sheet:
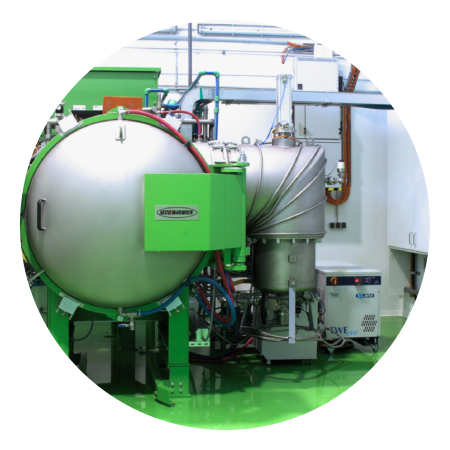
- Max. Temperature: 1200 °C
- Final vacuum (cold, baked furnace): <10–6 mbar
- Heating: Mo band heaters
- Radiation isolation: Mo and Stainless Steel